PROSPECTS OF USING POLYOLEFINS AS ALTERNATIVE STRUCTURAL MATERIALS FOR ULTRALIGHT LAUNCH VEHICLE
DOI:
https://doi.org/10.15421/jchemtech.v31i4.289212Keywords:
ultralight launch vehicle; polyethylene high density; polypropylene; physico-mechanical properties; thermal properties, high molecular weight compoundsAbstract
In the modern market of space launches, a clear demand for launch vehicles of light and ultralight classes for the prompt delivery of small-sized payloads into orbit formed. The solution to this problem lies in the search for new alternative structural materials that will ensure low cost and reliability of launches. This article substantiates the possibility of using polyethylene and polypropylene as an alternative material for the manufacture of shells of autophage rockets. In the work, based on the data known in the literature, the physical-mechanical, thermophysical and thermal properties, the advantages and disadvantages of these polymer materials analyzed. Four types of polyethylene (LDPE, HDPE, UHMWPE, PE-X), as well as three types of polypropylenes (PP, iso- and syndiotactic PP) considered. It is shown that, according to their mechanical and thermophysical characteristics, HDPE, UHMWPE, PE-X, PP have prospects for use as alternative structural materials for ultralight launch vehicles. The selected types of polyolefins characterized by high physical and mechanical characteristics and sufficiently high thermal properties. Further research of the characteristics of selected grades of polyolefins planned, considering the conditions of their operation as part of autophage rockets.
References
Dron’, M., Hilorme, T., Golubek, A., Dreus, A. (2022). Determining the performance indicators of employing combined methods for removing space objects from near-earth orbits. East.-Eur. J. Enterpr. Technol., 1(3-115), 6-12. https://doi.org/10.15587/1729-4061.2022.253096
Shoemaker, M. A., van der Ha, J. C., Abe, S., Fujita, K. (2013). Trajectory Estimation of the Hayabusa Spacecraft During Atmospheric Disintegration. J. Spacecr. Rockets, 50(2), 326–336. https://doi.org/10.2514/1.A32338
Smirnov, N. N., Kondratyev, K. A. (2009). Evaluation of craters formation in hypervelocity impact of debris particles on solid structures. Acta Astronaut., 65(11-12), 1796–1803. https://doi.org/10.1016/j.actaastro.2009.04.003
Fritsche, B., Klinkrad, H., Kashkovsky, A., Grinberg, E. (2000). Spacecraft disintegration during uncontrolled atmospheric Re-entry. Acta Astronaut., 47(2-9), 513–522. https://doi.org/10.1016/S0094-5765(00)00090-4
Balakrishnan, D., Kurian, J. (2014). Material Thermal Degradation Under Reentry Aerodynamic Heating. J. Spacecr. Rockets, 51(4), 1319–1328. https://doi.org/10.2514/1.A32712
Monogarov, K., Trushlyakov, V., Zharikov, K., Dron, M., Iordan, Yu., Davydovich, D., Melnikov, I., Pivkina, A. (2018). Utilization of thermite energy for re-entry disruption of detachable rocket elements made of composite polymeric material. Acta Astronaut., 150, 49-55. https://doi.org/10.1016/j.actaastro.2017.11.028
Dron M., Dreus A., Golubek A., Abramovsky Y. (2018). Investigation of aerodynamics heating of space debris object descending in earth atmosphere. Proc. 69th International Conference IAC-18, A6, IP, 39, Bremen, Germany. https://iafastro.directory/iac/archive/browse/IAC-18/A6/IP/43826/
Dreus A., Yemets V., Dron M., Yemets M., Golubek A. (2022). A simulation of the thermal environment of a plastic body of a new type of launch vehicle at the atmospheric phase of the trajectory. Aircraft Engineering and Aerospace Technology, 94(4), 505-514. https://doi.org/10.1108/AEAT-04-2021-0100
Amjadi, M., Fatemi, A. (2020). Creep and Fatigue Behaviors of High-Density Polyethylene (HDPE): Effects of Temperature, Mean Stress, Frequency, and Processing Technique. Int. J. Fatigue, 105871. https://doi.org/10.1016/j.ijfatigue.2020.105871
Amjadi, M., Fatemi, A. (2021). Creep behavior and modeling of high-density polyethylene (HDPE). Polym. Test., 94, 107031. https://doi.org/10.1016/j.polymertesting.2020.107031
Wu, H., Koo, J.H. (2022). Analysis of Flame Retardancy in Polymer Science. Chapter 8 – Characterization of high-temperature polymers for extreme environments. In H. Vahabi, M. Reza Saeb, G. Malucelli (Ed.). Elsevier. https://doi.org/10.1016/B978-0-12-824045-8.00008-3
Muthukumar, C., Krishnasamy, S., Thiagamani, S. M. K., Jeyaguru, S., Siengchin, S., Nagarajan, R. (2022). Encyclopedia of Materials: Plastics and Polymers. Polymer in Aerospace Applications. In M.S.J. Hashmi (Ed.). Elsevier. https://doi.org/10.1016/B978-0-12-820352-1.00077-8
Kryizhanovskiy, V. K., Burlov, V. V., Panimatchenko, Yu. V., Kryizhanovskaya Yu. V. (2005). [Technical properties of polymer materials (2nd ed.)]. Saint Petersburg, Russian Federation: Professiya (in Russian).
Spalding, M. A., Chatterjee, A. M. (Ed.). (2017). Handbook of industrial polyethylene and technology: definitive guide to manufacturing, properties, processing, application and markets. Hoboken, NJ: John Wiley & Sons.
Khattar, N., Jagriti, Ahlawat, V., Sharma, P., Berar, U., Diwan, P.K. (2023). Optimization of compression parameters of UHMWPE through thermal stability. Mater. Chem. Phys., 307, 128220. https://doi.org/10.1016/j.matchemphys.2023.128220
Balobanov, V., Verho, T., Heino, V., Ronkainen, H., Pelto, J. (2020). Micromechanical performance of high-density polyethylene: experimental and modeling approaches for HDPE and its alumina-nanocomposites. Polym. Test., 93, 10693 https://doi.org/10.1016/B978-1-895198-92-8.50002-1
Awad, A.H., El Gamasy R., Abd El Wahab, A., Abdellatif, M. H. (2019). Mechanical and Physical Properties of PP and HDPE. Engineering Science, 4(2), 34–42. doi:10.11648/j.es.20190402.12
Dixit, D., Pal, R., Kapoor, G., Stabenau, M. (2016). Lightweight composite materials processing. In A. Bhatnagar (Ed.), Lightweight Ballistic Composites (Second Edition, 157–216). Woodhead Publishing, Elsevier. https://doi.org/10.1016/B978-0-08-100406-7.00006-4.
Hartmann, B., Lee, G. F., Cole, R. F. Jr. (1986). Tensile yield in polyethylene. Polym. Eng. Sci., 26(8), 554–559. https://doi.org/10.1002/pen.760260806
Hartmann, B., Lee, G.F., Wong, W. (1987). Tensile yield in polypropylene. Polym. Eng. Sci., 27(11), 823–828. https://doi.org/10.1002/pen.760271109
Ministry of regional development and construction of Ukraine. (2008). [National standard of Ukraine]. (DSTU B.V. 2.7-143:2007). Kyiv, Minrehionbud Ukraine (in Ukrainian).
Amjadi, M., Fatemi, A. (2020). Creep and fatigue behaviors of High-Density Polyethylene (HDPE): Effects of temperature, mean stress, frequency, and processing technique. Int. J. Fatigue, 141, 105871. https://doi.org/10.1016/j.ijfatigue.2020.105871
Hartmann, B., Lee, G.F., Wong, W. (1987). Tensile yield in polypropylene. Polym. Eng. Sci., 27(11), 823–828. https://doi.org/10.1016/j.polymertesting.2020.106936
Polyakov, A. V. (Ed.) (1980). [Low-pressure polyethylene: Scientific and technical basis of industrial synthesis]. Leningrad, USSR: Khimiya (in Russian).
Rechytskyi, O. N., Reshnova, S. F. (2018). [Chemistry of high molecular weight compounds in schemes]. Kherson, Ukraine: Vyshemyrskyi V.S. (in Ukrainian).
Wypych, G. (2016). Handbook of Polymers (Second Edition). Toronto, ChemTecPublishing.
Yemets, V., Dron’, M., Kositsyna, O. (2019). Estimation of the possibilities for using the solid hydrocarbon fuels in autophage launch vehicle. Journal of Chemistry and Technologies, 27(1), 58–64. https://doi.org/10.15421/081906
Yemets, V., Dron, M., Pashkov, A., Dreus, A., Kositsyna, Y., Yemets, M., Dubovyk, L., Kostritsyn, O., Zhuravel, P. (2020). Method to Preset G-Load Profile of Launch Vehicles. 71th International Astronautical Congress. https://bit.ly/3rHbQUj
Kositsyna, O., Dron’, M., Yemets, V. (2020). The environmental impact assessment of emission from space launches: the promising propellants components selection. Journal of Chemistry and Technologies, 28(2), 186–193. https://doi.org/10.15421/082020
Kositsyna, O., Varlan, K., Dron, M., Kulik, O. (2021). Determining energetic characteristics and selecting environmentally friendly components for solid rocket propellants at the early stages of design. Eastern-European Journal of Enterprise Technologies, 6(114), 6–14. https://doi.org/10.15587/1729-4061.2021.247233
Yemets, V. (2008). Most effective areas for launch vehicles with combustible polyethylene tanks. Space science and technology, 14(1), 17–24. (in Ukrainian). https://doi.org/10.15407/knit2008.01.017
Yemets, V. (2010) The possibility of the effictive microlaunch vehicle realization by means of using its polymeric tank shell as fuel. Aerospace Technic and Technology, 10, 24–27. (in Ukrainian). http://nti.khai.edu:57772/csp/nauchportal/Arhiv/AKTT/2010/AKTT1010/Emec.pdf
Dreus, A., Dron, M., Dubovik, L., Strembovskyi, V. (2023). Assessment of the possibility of using polymers in the bodies of the promising launch vehicles based on the heat resistance factor. Space science and technology, 6(145), 3–12. https://doi.org/10.15407/knit2023.06.068
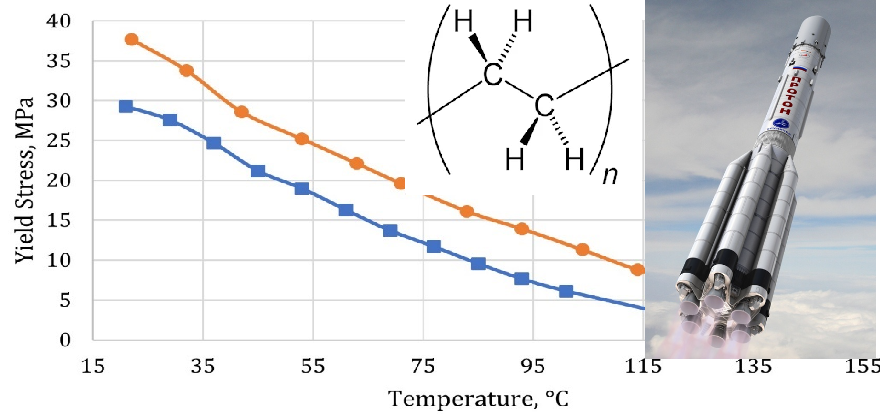
Downloads
Published
Issue
Section
License
Copyright (c) 2024 Oles Honchar Dnipro National University

This work is licensed under a Creative Commons Attribution 4.0 International License.
- Authors reserve the right of attribution for the submitted manuscript, while transferring to the Journal the right to publish the article under the Creative Commons Attribution License. This license allows free distribution of the published work under the condition of proper attribution of the original authors and the initial publication source (i.e. the Journal)
- Authors have the right to enter into separate agreements for additional non-exclusive distribution of the work in the form it was published in the Journal (such as publishing the article on the institutional website or as a part of a monograph), provided the original publication in this Journal is properly referenced
- The Journal allows and encourages online publication of the manuscripts (such as on personal web pages), even when such a manuscript is still under editorial consideration, since it allows for a productive scientific discussion and better citation dynamics (see The Effect of Open Access).