DEVELOPMENT OF DYEING TECHNOLOGY AND CREATION OF A BASIC TECHNOLOGICAL SCHEME FOR THE PROCESS OF REUSING CONCENTRATED WASTEWATER (ON THE EXAMPLE, REDUCING THE CONSUMPTION OF DIRECT YELLOW LIGHTFAST DYE K)
DOI:
https://doi.org/10.15421/jchemtech.v32i4.309831Keywords:
dyeing and finishing production, concentrated wastewater, reuse, resource-saving technology, direct dyes, coarse calico, viscose, schematic diagramAbstract
The development of wastewater reuse technology in fabric dyeing is a topical issue. This will minimise the use of water and expensive dyes, reduce the cost of finished products and the environmental impact. Concentrated wastewater from batch dyeing equipment contains up to 50% of textile dyes, so it can be reused as a secondary material resource in fabric dyeing technology. Рresents the results of studies of the efficiency of dyeing cotton fabrics with Direct Yellow Lightfast K dye with the reuse of concentrated wastewater: dye intensity 95–96 % compared to the standard (100 %), colour difference between the reference and test samples DE < 2, the lightness and shade indicators samples have a difference of ± 2, qualitative indicators of colour fastness are 3–4 points according to the «Grey Standard Scale. This results prove the effectiveness of dyeing cotton fabrics with Direct Yellow Lightfast K dye with the reuse of concentrated wastewater. A schematic diagram of cotton fabric dyeing technology was created. A technology for dyeing fabrics with the reuse of concentrated wastewater in the process of dyeing fabrics with direct dyes has been developed, with an average of 11 % savings in direct dye consumption per 1200 m of fabric. The dyeing according to this scheme has been tested at Private Joint Stock Company Cherkasy Silk Plant (Cherkasy, Ukraine). The spectrophotometric method was used in the course of the work; the durability of the staining was determined in accordance with the current state standards of Ukraine and international ISO standards; the Python programming language, Mathplotlib and Seaborn visualisation libraries were used to visualise the experimental data.
References
Cinperi, N.C., Ozturk, E., Yigit, N.O., Kitis, M. (2019). Treatment of woolen textile wastewater using membrane bioreactor, nanofiltration and reverse osmosis for reuse in production processes. Journal of Cleaner Production, 223, 837–848. https://doi.org/10.1016/j.jclepro.2019.03.166
Ntuli, F., Omoregbe, I., Kuipa, P., Muzenda, E., Belaid M. (2009). Characterization of effluent fromtextile wet finishing operations. WCECS 1, 37–48.
Periysamy, A.P., Militky, J. (2020). Sustainability in Textile Dyeing: Recent Developments. Sustainability in the Textile and Apparel Industries, 1(2), 37–79. https://link.springer.com/chapter /10.1007/978-3-030-38545-3_2
Behera, М., Nayak, J., Banerjee, S., Chakrabortty, S., Tripathy, S. K. (2021). A review on the treatment of textile industry waste effluents towards the development of efficient mitigation strategy: An integrated system design approach. Journal of Environmental Chemical Engineering, 9(4). https://doi.org/10.1016/j.jece.2021.105277
Lellis, B., Fávaro-Polonio, C.Z., Pamphile, J. A. (2019). Effects of textile dyes on health and the environment and bioremediation potential of living organisms. Biotechnol Res Innov. 3(2), 275–290. doi: 10.1016/j.biori.2019.09.001
Kishor, R., Purchase, D., Saratale, G.D., Saratale, R.G., Romanholo Ferreira, L.F., Bilal, M., Chandra, R., Bharagava, R. N. (2021). Ecotoxicological and health concerns of persistent coloring pollutants of textile industry wastewater and treatment approaches for environmental safety. Journal of Environmental Chemical Engineering, 9(2). https://doi.org/10.1016/j.jece.2020.105012
Efimov, A.Ya., Tavartkiladze, I.M., Tkachenko, L.I. (1985). [Wastewater treatment of light industry enterprises]. Kyiv: Technika. (in Ukrainian).
Singha, K., Pandit, P., Maity, S., Sharma, S. R. (2021). Chapter 11 - Harmful environmental effects for textile chemical dyeing practice. Green Chemistry for Sustainable Textiles. Modern Design and Approaches. The Textile Institute Book Series, 153–164. https://doi.org/10.1016/B978-0-323-85204-3.00005-1
Zaharia, C., Suteu, D. (2012). Textile Organic Dyes – Characteristics, Polluting Effects and Separation. Environmental and analytical update, 55–86. https://doi.org 10.5772/32373
Srebrenkoska, V., Zhezhova, S., Risteski, S., Saska, G. (2014). Methods for waste waters treatment in Textile Industry. UNITECH 2014, 248-252.
Bergenthal, J., Hendriks, R., Tincher, W., Eapen, J., Tawa, A. (1984). Textile Dyebath Reconstitution and Reuse. The EPA National Library Catalog | EPA National Library Network | US EPA
Bergenthal, J., Eapen, J., Hendriks, R., Tawa, A., Tincher, W. (1985). Fulle-scale emonstration of Textile Dye wastewater reuse. Conf. 40th waste conf., 165-171.
Chiarello, L.M., Mittersteiner, M., Cesar de Jesus, P., Andreaus, J., Barcellos, I.O. (2020). Reuse of enzymatically treated reactive dyeing baths: Evaluation of the number of reuse cycles. Journal of Cleaner Production. 267. https://doi.org/10.1016/j.jclepro.2020.122033
Hossain, A., Ak, S. (2019). A cost minimization process of heat and energy consumption for direct dyeing of cotton fabric coloration with triethanolamine. Textile Eng Fashion Technol. 5(5), 235–240. doi: 10.15406/jteft.2019.05.00207
Buscio, V., García-Jiménez, M., Vilaseca, M., López-Grimau, V., Crespi, M., Gutiérrez-Bouzán, C. (2016). Reuse of Textile Dyeing Effluents Treated with Coupled Nanofiltration and Electrochemical Processes. Academic Open Access Publishing. 9(6), 490–512. https://doi.org/10.3390/ma9060490
Fomina, N.M., Koval, M.G., Azizov, F.R., Stolyarenko, G.S. (2019). [Investigation of the possibility of using cavitation processes in the development of promising technology for cleaning wastewater dyeing and finishing production and their reuse]. Polytechnic Bulletin- Dushanbe: ed. TTU, 1(45) 135–141. (in Russian).
Koval, M.G. (2022). [Planning and organisation of experimental studies of the cyclic use of resources in the technology of dyeing textile materials (on the example of dispersed dark blue Z dye)]. Scientific Notes of Vernadsky TNU. Series: Technical Sciences, 33 (72) 203–209. (in Ukrainian). doi https://doi.org/10.32782/2663-5941/2022.6/32
Kaushik, C.P., Ravinder, T. N., Kaushik, J.K., Gaurav, S. (2009). Minimization of organic chemical load in direct dyes effluent using low cost adsorbents. Chemical Engineering Journal, 155(1-2), 234–240. doi: 10.1016/j.cej.2009.07.042.
Direct Yellow R. PubChem. https://pubchem.ncbi.nlm.nih.gov/compound/18576
Burkinshaw S.M. (2021). The role of inorganic electrolyte (salt) in cellulosic fibre dyeing: Part 1 fundamental aspects. Coloration Technology, 137, (5), 421–444. https://doi.org/10.1111/cote.12547
Korabayev, S., Kozakov, F., Sharifjonov, I., Abdulhakova, S. (2021). Analysis of the properties of the coarse calico fabric. Collection of scientific papers Λ'OΓOΣ. Coference proceedings. doi: 10.36074/logos-30.04.2021.v1.48
Yermakova, A. (2023). Detailed description of the fabric calico. https://marry.in.ua/detalnyy -opys-tkanyny-byaz/
Roux, C., Robertson, J. (2000). Fibers/Types. Encyclopedia of Forensic Sciences. 838–854.
https://doi.org/10.1006/rwfs.2000.0513
Halbeisen, M. (2005). Textiles/Natural. Encyclopedia of Analytical Science (Second Edition) 1–8. https://doi.org/10.1016/B0-12-369397-7/00611-7
Alter, L. (2022). What Is Viscose and How Is It Made? https://www.treehugger.com/what-is-viscose-fabric-5070642
State Standard of Ukraine. Materials and products of textile, knitted, sewing and leather. Terms and definitions. (2001). (DSTU 3998-2000) http://online.budstandart.com/ru/catalog/document.html?iddoc=94911. Kyiv, Ukraine.
International Standard. Textile materials. Determination of colour fastness. Part X12. Method for determining the friction resistance of colouring. (2016). (DSTU ISO 105-Х12:2016). International Organization for Standardization. Technical Committee ISO/TC 38, Textiles. Geneva, Switzerland.
International Standard. Textile materials. Determination of colour fastness. Part A02. Grey scale for assessing colour change. (2005). (DSTU ISO 105 А02:2005). International Organization for Standardization. Geneva, Switzerland.
International Standard. Materials are textile. Test method for colour fastness. Part C10. Colour fastness to washing with soap or soap and soda (2007) ((DSTU EN ISO 105-C10:2020 (EN ISO 105-C10:2007, IDT; ISO 105-C10:2006, IDT)). Geneva, Switzerland.
Hernandez, B., Saenz, C., Alberdi, C., Dineiro, J.M. (2016). CIELAB color coordinates versus relative proportions of myoglobin redox forms in the description of fresh meat appearance. Journal of Food Science and Technology. 53 (12), 4159–4167. doi: 10.1007/s13197-016-2394-6
Colorimetric Fundamentals CIELab. Certified to ISO 9001 in Manufacturing Centers Worldwide. https://www.datacolor.com/wp-content/uploads/2022/11/color_fundamentals_part_ii.pdf
Gaurav, S., Raja, B. (2003). Digital Color Imaging Handbook. CRC Press.
Koval, M., Romanenko, N. (2022). [The principle of wastewater reuse in textile dyeing processes]. Technical Sciences and Technologies, 4(30), 169–179. https://doi.org/10.25140/2411-5363-2022-4(30)-169-179 (in Ukrainian).
Koval, M.G., Feshchenko, N.V. (2022). [Investigation of the process of dyeing cotton fabrics with direct blue dye DIRECT B2RL using wastewater]. The 12th International scientific and practical conference “Modern science: innovations and prospects”, Stockholm, Sweden., 84–88. (in Ukrainian).
Koval, M. (2023). [An innovative approach to creating a resource-saving technology for dyeing textile materials]. Synergy of science and business in the post-war restoration of Kherson region, 327- 331. (in Ukrainian).
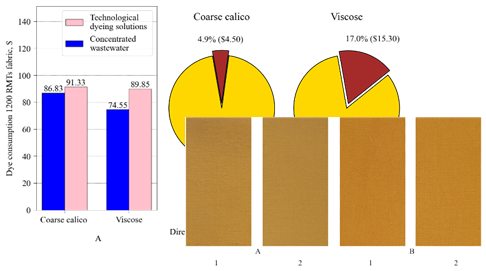
Downloads
Published
Issue
Section
License
Copyright (c) 2024 Oles Honchar Dnipro National University

This work is licensed under a Creative Commons Attribution 4.0 International License.
- Authors reserve the right of attribution for the submitted manuscript, while transferring to the Journal the right to publish the article under the Creative Commons Attribution License. This license allows free distribution of the published work under the condition of proper attribution of the original authors and the initial publication source (i.e. the Journal)
- Authors have the right to enter into separate agreements for additional non-exclusive distribution of the work in the form it was published in the Journal (such as publishing the article on the institutional website or as a part of a monograph), provided the original publication in this Journal is properly referenced
- The Journal allows and encourages online publication of the manuscripts (such as on personal web pages), even when such a manuscript is still under editorial consideration, since it allows for a productive scientific discussion and better citation dynamics (see The Effect of Open Access).