RECYCLING OF WC-Ni SCRAP TO OBTAIN TUNGSTEN CARBIDE
DOI:
https://doi.org/10.15421/jchemtech.v32i3.309294Keywords:
powdered tungsten carbide; binder; self-grinding; recycling; leaching degree.Abstract
The paper is devoted to the relevant issue of recycling scrap of the strategic WC-Ni alloy used in the production of armor-piercing shells. The recycling of tungsten and nickel carbide eliminates the problem of shortage and high cost of these components. This paper investigates the effect of the concentration of hydrochloric acid and iron (III) chloride in the leaching solution on the extent of nickel leaching from cemented tungsten carbide. It was found that an increase in the concentration of both components leads to an increase in the process rate. It has been shown that the addition of iron (III) chloride to the acid leaching solution leads to a fivefold increase in the process rate. It has been established that the activation energy of the leaching process in a solution of 4.5 mol/L chloride acid is 50.5 kJ/mol. The activation energy of leaching in a solution containing 4.5 mol/L hydrochloric acid and 2 mol/L iron (III) chloride is 17.9 kJ/mol. When switching from an acid leach solution to a solution containing a mixture of acid and iron (III) chloride, the process moves from the kinetic to the diffusion region. To accelerate leaching under conditions of diffusion limitations, it is proposed to increase the efficiency of surface renewal of raw material pieces by selecting the size and rotation frequency of the grinding drum. It has been shown that the dependence of the leaching degree on the drum rotation frequency passes through a maximum. Increasing the diameter of the drum increases the leaching degree. A new method for leaching a WС-Ni composite to obtain high-quality tungsten carbide powder has been proposed. The process intensification is achieved by organizing leaching under self-grinding conditions with continuous mechanical renewal of the surface that is in contact with the leaching solution.
References
Polini, R., Marcucci, A., D’Ottavi, C., Nunziante, P., De Filippis, P., Marcheselli, G. (2021). Toward Greener Synthesis of WC Powders for Cemented Tungsten Carbides Manufacturing. ACS Sustainable Chemistry & Engineering, 9(25), 8458–8466. doi:10.1021/acssuschemeng.1c01286
Shen, L., Li, X., Lindberg, D., Taskinen, P. (2019). Tungsten extractive metallurgy: A review of processes and their challenges for sustainability. Minerals Engineering, 142, 105934. doi:10.1016/j.mineng.2019.105934
Byun, S.Y., Park, J. S., Kang, J. H., Seo, S., Tran, T., Kim, M. J. (2021). Recovery of tungsten and cobalt from cemented tungsten carbide wastes using carbonate roasting and water leaching. Journal of the Air & Waste Management Association, 71(6), 711–720. doi:10.1080/10962247.2021.1876780
Rizzo, A., Goel, S.; Luisa Grilli, M., Iglesias, R., Jaworska, L., Lapkovskis, V., Novak, P., Postolnyi, B.O., Valerini, D. (2020). The Critical Raw Materials in Cutting Tools for Machining Applications: A Review. Materials, 13, 1377.
Kumar, R., Kariminejad, A., Antonov, M., Goljandin, D., Klimczyk, P., Hussainova, I. (2023). Progress in Sustainable Recycling and Circular Economy of Tungsten Carbide Hard Metal Scraps for Industry 5.0 and Onwards. Sustainability, Sustainability, 15, 12249. https://doi.org/10.3390/su151612249
Shemi, A., Magumise, A., Ndlovu, S., Sacks, N. (2018). Recycling of tungsten carbide scrap metal: A review of recycling methods and future prospects. Minerals Engineering, 122, 195–205. doi:10.1016/j.mineng.2018.03.036
Furberg, A., Arvidsson, R., Molander, S. (2019). Environmental life cycle assessment of cemented carbide (WC-Co) production. Journal of Cleaner Production, 209, 1126–1138. doi:10.1016/j.jclepro.2018.10.272
Yang, L., Li, C., Cao, C., Xue, X., Gong, D., Wan, L. (2022). Kinetics of Low-Grade Scheelite Leaching with a Mixture of Sodium Phosphate and Sodium Fluoride. Metals, 12, 1759. https://doi.org/10.3390/met12101759
Baba, A. A., Kayode, J. O., Raji, M. A. (2020). Low-Energy Feasibility for Leaching an Indigenous Scheelite Ore for Industrial Applications. Journal of Sustainable Metallurgy, 6(4), 659–666. doi:10.1007/s40
Ren, H., Li, J., Tang, Z., Zhao, Z., Chen, X., Liu, X., He, L. (2020). Sustainable and efficient extracting of tin and tungsten from wolframite – scheelite mixed ore with high tin content. Journal of Cleaner Production, 269, 122282. doi:10.1016/j.jclepro.2020.122282831-020-00301-7
Li, J., Ma, Z., Liu, X., Chen, X., Zhao, Z. (2020). Sustainable and Efficient Recovery of Tungsten from Wolframite in a Sulfuric Acid and Phosphoric Acid Mixed System. ACS Sustainable Chemistry & Engineering. 8(36), 13583–13592. doi:10.1021/acssuschemeng.0c04216
Katiyar, P. K., Randhawa, N. S. (2020). A comprehensive review on recycling methods for cemented tungsten carbide scraps highlighting the electrochemical techniques. International Journal of Refractory Metals and Hard Materials, 90, 105251. doi:10.1016/j.ijrmhm.2020.105251
Liu, B., Shi, A., Su, Q., Chen, G., Li, W., Zhang, L., Yang, B. (2017). Recovery of tungsten carbides to prepare the ultrafine WC-Co composite powder by two-step reduction process. Powder Technology, 306, 113–119. doi:10.1016/j.powtec.2016.10.071
Fremantle, C., N. Sacks. (2015). Recycling of cemented tungsten carbide mining tool scrap. J. South Afr. Inst. Mining Metal 115(12), 1207–13. doi:10.17159/2411-9717/ 2015/v115n12a9.
Zhang, L., Nie, Z., Xi, X., Ma, L., Xiao, X., Li, M. (2017). Electrochemical Dissolution of Tungsten Carbide in NaCl-KCl-Na2WO4 Molten Salt. Metallurgical and Materials Transactions B, 49(1), 334–340. doi:10.1007/s11663-017-1125-3
Li, M., Xi, X., Liu, Q., Nie, Z., Ma, L. (2019). Direct electrolytic separation of tungsten and cobalt from waste cemented carbide and electrochemical behavior of tungsten and cobalt ions in NaF–KF molten salts. Journal of Electroanalytical Chemistry, 833, 480–489. doi:10.1016/j.jelechem.2018.12.03
Xiao, X., Xi, X., Nie, Z., Zhang, L., Ma, L. (2016). Direct Electrochemical Preparation of Cobalt, Tungsten, and Tungsten Carbide from Cemented Carbide Scrap. Metallurgical and Materials Transactions B, 48(1), 692–700. doi:10.1007/s11663-016-0836-1
Gurmen, S. (2005). Recovery of nano-sized cobalt powder from cemented carbide scrap. Turk. J. Eng. Environ. Sci. 29, 343–350.
Seo, B., Kim, S. (2016). Cobalt extraction from tungsten carbide-cobalt (WC-Co) hard metal scraps using malic acid. International Journal of Mineral Processing, 151, 1–7. doi:10.1016/j.minpro.2016.04.002
Lee, J., Kim, M., Kim, S., Ahn, Y., Lee, B., Lee, D. (2021). Facile recycling of cemented tungsten carbide soft scrap via mechanochemical ball milling. International Journal of Refractory Metals and Hard Materials, 100, 105645. doi:10.1016/j.ijrmhm.2021.105645
Baláž, P., Achimovicová, M., Baláž, M., Billik, P., Zara, C.Z., Criado, J.M., Delogu, F., Dutková, E., Gaffet, E., Gotor, F.J., Kumar, R., Mitov, I., Rojac, T., Senna M., Streletskii, A., Wieczorek-Ciurowa, K. (2013). Hallmarks of mechanochemistry: From nanoparticles to technology. Chem. Soc. Rev., 42, 7571–7637.
doi: 10.1039/c3cs35468g
Zhu, X.; Liu, X.; Zhao, Z. (2019). Leaching kinetics of scheelite with sodium phytate. Hydrometallurgy, 186, 83–90. doi:10.1016/j.hydromet.2019.04.004
Li, T.-T., Shen, Y.-B., Zhao, S.-K., Yin, Y.-Y., Lu, R., Gao, S.-L., Han, C., Wei, D.-Z. (2019). Leaching kinetics of scheelite concentrate with sodium hydroxide in the presence of phosphate. Trans. Nonferrous Met. Soc. China, 29, 634–640. doi:10.1016/s1003-6326(19)64973-3
Mulenshi, J.; Chelgani, S.C.; Rosenkranz, J. (2021). Mechanochemical Treatment of Historical Tungsten Tailings: Leaching While Grinding for Tungsten Extraction Using NaOH. Sustainability, 13, 3258. https://doi.org/10.3390/su13063258
Mikhailov, I.F., Baturin, A.A., Mikhailov, A.I., Fomina, L. P. (2016). Perspectives of development of X-ray analysis for material composition, Funct. Mater. 23, 5–14.
Sknar, Y.E., Amirulloeva, N.V., Sknar, I.V., Danylov, F.I. (2016). Electrodeposition of Ni–ZrO2 Nanocomposites from Methanesulfonate Electrolytes, Materials Science, 51(6), 877–884. doi:10.1007/s11003-016-9916-2
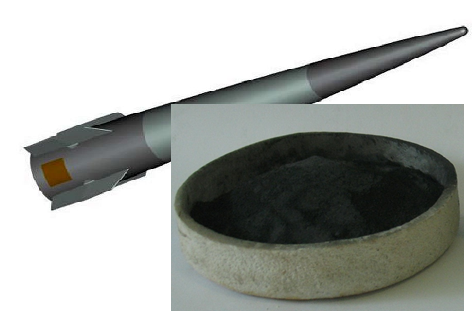
Downloads
Published
Issue
Section
License
Copyright (c) 2024 Oles Honchar Dnipro National University

This work is licensed under a Creative Commons Attribution 4.0 International License.
- Authors reserve the right of attribution for the submitted manuscript, while transferring to the Journal the right to publish the article under the Creative Commons Attribution License. This license allows free distribution of the published work under the condition of proper attribution of the original authors and the initial publication source (i.e. the Journal)
- Authors have the right to enter into separate agreements for additional non-exclusive distribution of the work in the form it was published in the Journal (such as publishing the article on the institutional website or as a part of a monograph), provided the original publication in this Journal is properly referenced
- The Journal allows and encourages online publication of the manuscripts (such as on personal web pages), even when such a manuscript is still under editorial consideration, since it allows for a productive scientific discussion and better citation dynamics (see The Effect of Open Access).